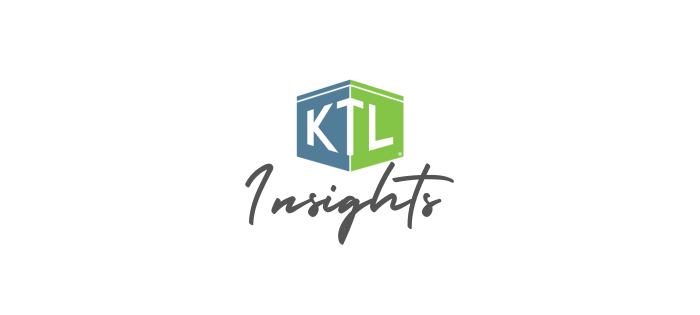
Safety
Comments: No Comments
A recent episode of The Daily, a podcast from The New York Times, discussed the safety culture of the Boeing manufacturing plant in Charleston, South Carolina—the plant that builds the 737 MAX 8, the aircraft involved in two fatal crashes worldwide in the last six months.
Concerns About Culture
The Boeing 737 MAX 8 was grounded by the FAA on March 11, 2019 amid concerns that recently introduced flight control software contributed to both crashes. The subsequent scrutiny on the company brought attention to the safety culture of the Charleston plant.
Interviews in the podcast suggest common characteristics of a negative safety culture were present at Boeing. For example, there was reportedly significant pressure to meet production deadlines, including financial incentives for meeting hourly production goals. Some managers allegedly took defective parts and installed them on aircraft to meet these deadlines. One such incident described on the podcast episode included an attempt to rub off the red paint that is applied to defective parts to prevent installation. Related to defective parts, managers were reportedly pressured to reduce the number of parts damaged by employees during manufacturing. A former quality manager interviewed in the episode alleges that this pressure led to damaged parts being installed rather than reported to management or quality control.
Safety culture is often defined informally as “the way we do things around here” when it comes to safety practices. Essentially, safety culture is the product of the shared values, beliefs, norms, and organizational practices in a company about working safely. An organization’s safety culture is ultimately reflected in the way safety is managed in the workplace. The culture breaks down when the disregard for safety becomes “management practice.”
Characteristics of a Strong Safety Culture
A strong safety culture has several characteristics in common. Kestrel’s research into the topic of safety culture has identified two traits that are particularly important to an effective safety culture: leadership and employee engagement. Best-in-class safety cultures have robust systems in place to ensure that each of these traits, among others, is mature, well-functioning, and fully ingrained into the standard practices of the organization.
Organizations with strong safety cultures typically exhibit many of the following attributes:
- Communication. Communication is most effective when it comprises a combination of top-down and bottom-up interaction. Senior management sets the strategic goals and vision for the company’s safety program. It is vital that all levels of management (senior, middle, supervisory) communicate the strategy clearly to the workers who carry out the company’s mission. It is equally important that workers provide feedback on a practical level about what’s working and what’s not.
- Commitment. When it comes to safety, actions truly speak louder than words. A lack of commitment, as demonstrated by action (or lack thereof), comes across loud and clear to staff. For example, requiring staff to work excessive hours or use defective parts to meet productivity goals sends a clear message that productivity is more important than safety.
- Caring. Caring is about doing whatever is necessary to ensure employees return home safely every night. It involves showing concern for the personal safety of individuals, not just making a commitment to the overall idea of safety.
- Cooperation. Safety works best if management and workers are on the same team. Cooperation means working together to develop a strong safety program (e.g., management involving line workers in creating safety policies and procedures). It means management seeks feedback from workers about safety issues—and uses that feedback to make improvements. And it means there is no blame when incidents occur.
- Coaching. Coaching each other—peer to peer, supervisor to employee, even employee to management—is an important way to keep everyone on track. Coaching involves non-judgmentally providing feedback for improvements and, correspondingly, accepting and incorporating that feedback as constructive criticism.
- Procedures. There should be documented, clear procedures for every task. This not only prevents disagreement about what is required, it also shows commitment when things are put in writing. Procedures should be designed jointly by management and workers for practicality and to encourage improved cooperation, communication, and buy-in.
- Training. Training is a more formal, documented process for ensuring that employees follow safety processes and procedures. Formal training should happen frequently enough for employees to feel prepared to safely do their jobs.
- Tools. All equipment and tools should be in good repair, free of debris, and functioning as designed. Inadequate tools directly impact safety/protection and indirectly impact perception of management commitment. Boeing’s alleged practices send a clear message that safety is not as important as productivity.
- Personnel. There must be enough workers to do each task safely. The company should not sacrifice individual safety because of being understaffed (i.e., requiring shortcuts/overtime to meet production goals).
- Trust. Trust in the safety program, in senior management, and in each other is built when each of these characteristics is present and treated as a company-wide priority.
Benefits of a Best-in-Class Safety Culture
Strong safety performance is a cornerstone of any business. When these characteristics come together to create a best-in-class safety culture, everyone wins:
- Fewer accidents, losses, and disruptions
- Improved employee morale
- Increased productivity
- Lower workers compensation and insurance claims
- Improved compliance with OSHA regulations
- Improved reputation to attract new customers and employees and retain existing ones
- Better brand and shareholder value