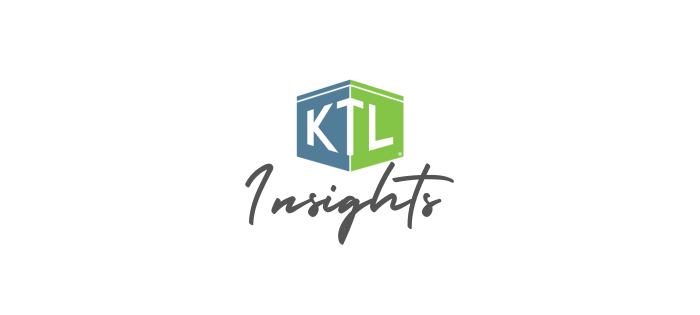
Technology Enabled Business Solutions
Comments: No Comments
This is the next article in Kestrel’s series about Technology-Enabled Business Solutions.
What do you do when your company has multiple grandfathered-in systems that don’t talk to each other? How about when not all locations have access to the same systems…and you have over 150 locations and are still growing? What about when employees are spending excess time collecting and combining information manually instead of electronically? What if you can’t correlate data and generate reports because of multiple systems?
Cut Your Losses, Prioritize Your Needs
These things happen—probably more frequently than one might think. For one of Kestrel’s clients, a large chemical distribution company, all these things were happening simultaneously, and the cost to upgrade existing systems to respond to these needs was getting out of hand. How do you manage that? Do you just cut your losses and find a new compliance IMS solution? Do you address one issue at a time, or does that introduce the risk that everything won’t work together? Again.
Transitioning from one system to another—whether in part or completely—isn’t simple. It takes planning and forethought to create a scalable solution that can be adapted to the company’s overall needs. Proactively managing any sort of technology transition—including prioritizing needs and scheduling how quickly modules are developed and rolled out—is key.
From the beginning, Kestrel’s EHS and IT consultants worked to fully understand the company’s operations, existing systems and workflows, and desired outcomes of the overall system before recommending an approach. Without these upfront conversations, this company could’ve ended back in the same situation with a different system. Instead, they are on their way to developing a robust and scalable compliance IMS that can be adapted to the company’s overall needs and will eventually replace their off-the-shelf software.
Starting with the Data
Our client’s initial request was for dashboard reporting that would:
- Provide a visual of the Excel reports the company was pulling from multiple independent systems, and
- Create efficiencies in the data collection and reporting approach.
During initial conversations about the company’s compliance, information management, and overall business needs, it became clear to Kestrel that the existing facility database forms the foundation for the overall system. All content stems from this database. To create the efficiencies and dashboards the company wanted, building the facility database needed to happen first.
Facility information was originally tracked on individual Excel spreadsheets that were later combined to create a quarterly report. This very manual practice presented risks of user error in data entry, data manipulation, analysis, and reporting. Kestrel developed a facility database in SharePoint to serve as a centralized list, with detailed information on each location. Multiple other databases were then created that filter content into each facility page to create a simplified view of all items associated with each facility. Those other databases currently include:
- Employee counts
- Facility audits
- Sustainability reports
- List of storage tanks, with other assets to be added in the future
- Facility images
- Managed requirements
Let’s look at the employee database as one example of data that flows into the facility database. The employee database is used to track the number of employees in each location and each department. Information is filtered into the facility database, updating the employee count section. This employee database is also used to track access/permissions to the company site, look up individuals within other forms, and assign training based on job title.
The facility database now acts as the centralized core to the entire system. Information available here can be used to drive other actions and lists within the site, such as compliance tasks, corrective and preventive actions (CAPAs), inspections, near-misses, incidents, permitting requirements, etc.
Bringing in Forms
Where does all the data in those databases come from? That is where mobile forms and checklists enter the picture. Integrating various Office 365 technologies, Kestrel is creating several mobile forms, such as the near-miss app, to allow employees in the field to capture data electronically. The forms are accessible at multiple levels and can be assigned down to an individual location. Importantly, there is no need to log in to submit data, ensuring ease of access and use for all employees.
As employees complete the forms, data is collected and uploaded into the company’s related database(s) in real-time. All forms and databases are integrated. Not only does this eliminate the problems associated with manual data entry and manipulation, it provides real-time access to valuable data.
Compliance Dashboard
Kestrel has also created a login-driven compliance dashboard that houses key metrics, compliance tasks, and an at-a-glance compliance calendar. The dashboard can be customized for various applications based on the company’s needs as they continue to use the system—employees, management, departments, divisions, facilities, etc.
Currently, various compliance tasks (and associated reminders) are assigned to individuals throughout the 150+ locations. The dashboard filters assigned tasks to the individual logged in, so each employee can view his/her compliance-related tasks. At the same time, management can view outstanding issues that fall under their area(s) of responsibility, and the calendar provides a quick overview of compliance deadlines throughout the year.
The dashboard provides additional visibility for compliance tasks and alerts management to issues that need attention/resolution across the organization. It can also incorporate data analytics to help identify patterns and trends, inform business decisions, and guide resources.
Building for the Future
Now that the company has a solid foundation, work can commence to bring the independent systems into a single platform. Kestrel’s EHS team continues to identify additional compliance management needs, including checklists and mobile forms, internal audits, permit tracking, training tracking, safety meetings, mobile inspection/audit functionality, document control, incident reporting, and more. As these needs are identified, they can be built into the larger compliance IMS to create one integrated system going forward.
As Kestrel’s lead SharePoint Specialist Jaime Doty stated in a recent Q&A, “If you know where you want to end in an ideal world, it becomes a lot easier to find the starting point. It also makes creating a scalable system much more likely, because you are designing the system with the end in mind.”
This has ensured development of a system that:
- Is built from the perspective of the people who will be using them—in the field, in the plant, in the office, in the board room
- Integrates various databases and forms into a single, familiar platform
- Allows information to be shared and tracked in multiple ways
- Gives the ability to manage sites/facilities/plants/departments for compliance purposes
- Simplifies the data entry process by providing user-friendly functionality
- Provides for continual adaptation to meet future data management and reporting needs
That is exactly the forward-thinking perspective Kestrel takes on all projects—thinking beyond individual efficiency tools, considering the desired state, and determining how technology can make that happen. By coordinating technology and compliance expertise, Kestrel offers unique capabilities and perspective. Our EHS and food safety professionals understand the regulatory obligations, business needs, and needs of the users. This drives design and development of the right compliance IMS and efficiency tools—one that works within the company’s implementation timeline and budget—to reduce compliance risk, create operational efficiencies, and generate business improvement and value.