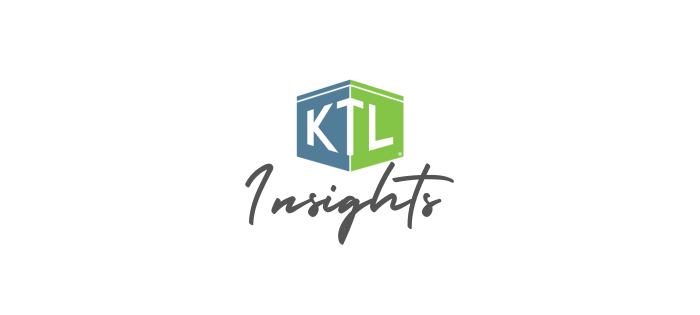
Food Safety
Comments: No Comments
Every food product and service company has an obligation to its customers to provide safe and quality food. A well-designed and well-executed food safety auditing program—with data trend analysis—provides an important tool for ensuring food safety. Auditing captures compliance status, Food Safety Management System conformance, adequacy of internal controls, potential risks, and best practices.
Combining effective auditing program design, standardized procedures, trained/knowledgeable auditors, and information technology systems and tools helps to ensure that food companies have the resources needed to get the most out of their food safety audits.
These resources may include:
- A reliable tool for conducting certification audits
- A systematic method of tracking audit status, schedule, and auditor capabilities
- Detailed audit and nonconformance data trending to help focus on risk areas for improvement
- Tracking of corrective actions
- Reports on performance metrics that allow the company to demonstrate compliance with regulatory requirements, evaluate trends, and make management decisions
The goal should be to effectively capture and analyze audit data and then use that information to improve food safety and quality, achieve certification requirements, and enhance overall business performance.
Technology Integration: Case Study
The following case study shows how integrating information technology into the auditing process can enhance data collection, analysis, and reporting capabilities.
This food manufacturer wanted to better track and manage its audit status and use the data collected to help focus on risk areas for improvement. Working with Kestrel’s food safety and IT experts, the company decided to use dynaQ™, Kestrel’s web-based assessment tool.
Kestrel took the following project approach to ensure that the company would be able to efficiently conduct its audits and, just as important, analyze audit data to uncover areas of nonconformance and opportunities to improve performance and reduce business risks.
Part 1: Project Kickoff – Identify and define initial dynaQ™ configuration, customization, training, and implementation scopes. Kestrel customized the existing platform to create nearly custom software to meet the organization’s needs.
Part 2: Project Launch and Training – Provide intensive training to ensure key staff knows how to conduct relevant inspections and are versed on reporting and data trends. At the end of the training session, staff was ready to work independently with dynaQ™.
Part 3: Implementation and Project Support – Continue training users on the dynaQ™ auditing process and provide ongoing support. The key factor in any audit program’s success is staff adoption. Ongoing support ensures that the company realizes maximum benefit.
Implementation has involved using dynaQ™ to facilitate a number of activities:
- Collect and analyze data from:
- Daily pre-op and ATP inspections
- Monthly GMP and glass & brittle plastic inspections
- Twice daily operations inspections
- ISO 22000 conformance audits under FSSC22000
- ISO/TS22002-1 conformance audits
- Create a new form and process to facilitate the nature of quality evaluations, using dynaQ™ to compile the results
- Track noncompliance records (NRs) as the plant is notified
By integrating information technology into the auditing process, this two-month pilot project has resulted in the following benefits to the company:
- More effective pre-op
- Increased line utilization
- Immediate QA evaluation capability
- Improved efficiency and speed of data collection and report generation
- Enhanced ability to demonstrate compliance with regulatory requirements, evaluate trends, and make management decisions
- Improved data security