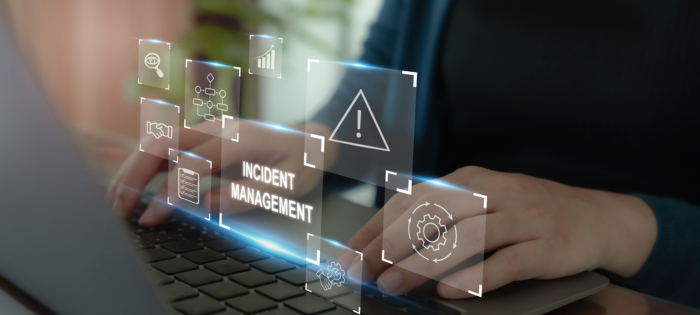
Tech Corner: Incident Management Tool
Functionality: What does it do?
Every organization is at risk of incidents, those unplanned events that have the potential to disrupt service and cause significant operational impacts—safety, environmental, food safety, quality, reputational, etc. KTL’s Incident Management Tool provides organizations with an effective system to help manage workplace incidents, track patterns, identify trends, and correct unsafe practices to maintain compliance and prevent future issues.
Benefits: Why do you need it?
Built on Microsoft’s Power Platform, KTL’s Incident Management Tool:
- Allows for easy and secure data entry from any device, anytime, anywhere with mobile access.
- Tracks all types of incidents in one system, providing centralized incident data management, trending, and analysis.
- Connects to KTL’s Root Cause Analysis Tool and Corrective and Preventive Action (CAPA) Tracking Log to enhance incident investigations, identify root causes, and track and manage CAPAs to closure.
- Implements workflows to manage incidents, including sending email notifications, routing documents, processing forms, etc.
- Generates customized dashboards that provide visual displays of incident data to help identify opportunities to prevent future incidents.
- Improves compliance by organizing data for reporting to OSHA, EPA, or other regulatory agencies.
- Allows response teams to document and share information as events unfold—from initial emergency response protocols through crisis management steps—so proper decisions can be made and documented for business continuity.
Technology Used
- Power Apps
- Microsoft Dataverse
- Power Automate
- Power BI
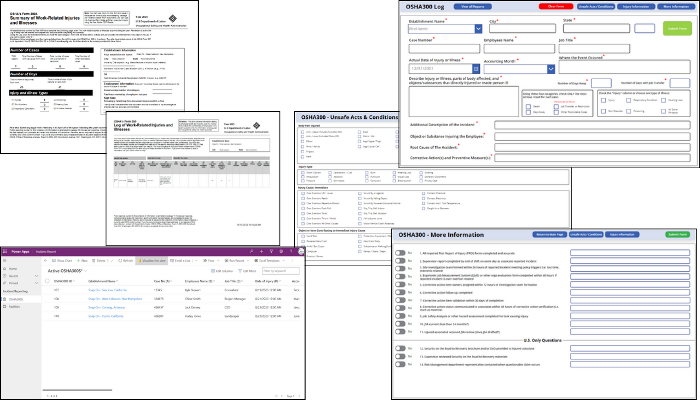
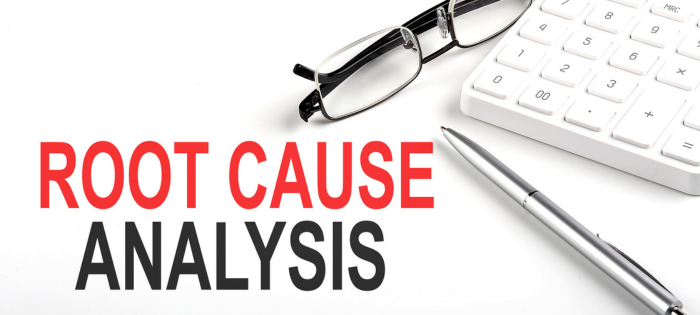
Tech Corner: Root Cause Analysis Tool
Functionality: What does it do?
Root cause analysis (RCA) is a systematic method of problem-solving used to identify the underlying (i.e., root) cause(s) of a problem or incident, alleviate risk, and help ensure that similar problems do not occur in the future. KTL’s RCA Tool walks users through the 5-Why Process, a simple method for conducting an RCA that involves asking the question “Why” enough times (i.e., five times) to get past the symptoms of a problem and down to the underlying root cause of the issue.
Benefits: Why do you need it?
KTL’s RCA Tool ties directly to corrective and preventive actions (CAPAs) to help ensure an RCA is conducted, as needed, for each CAPA. The tool sends a notification to supervisor/management when a CAPA is submitted with a direct link to the CAPA so management can complete the RCA, assigns follow-up actions and sends notifications to the responsible person(s), and keeps records in a central location for audits, regulatory visits, or future data analysis.
Using the RCA Tool offers a simple way to conduct an effective RCA that can help organizations to:
- Reduce the risk of injury and/or death to workers and community members.
- Avoid unnecessary costs resulting from business interruption; emergency response and cleanup; increased regulation, audits, and inspections; and OSHA fines.
- More effectively control hazards, improve process reliability, increase revenues, decrease production costs, lower maintenance costs, and lower insurance premiums.
Technology Used
- SharePoint for data storage
- Power Apps for the user interface
- Power Automate to send notifications
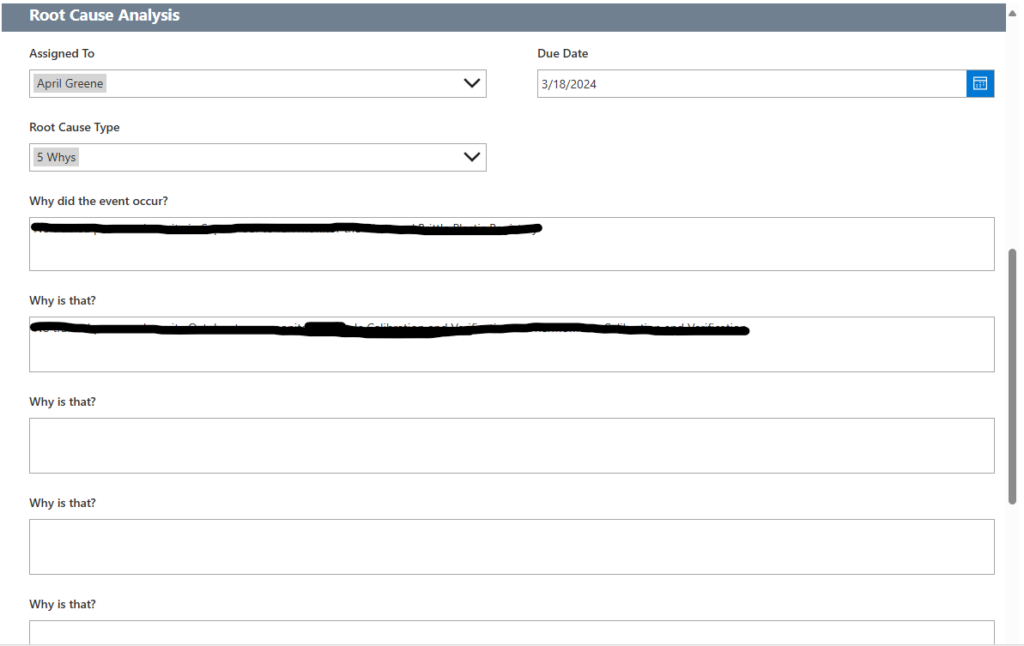
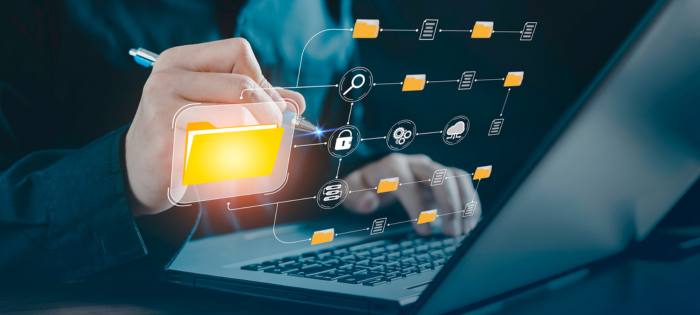
Tech Corner: Using SharePoint as a Management Tool
Functionality: What does it do?
Having a simple, centralized system to manage, track, communicate, and report compliance program information can enable staff to complete required tasks, improve compliance performance, and support operational decision-making. Microsoft SharePoint® provides a powerful platform that helps organizations manage, share, and collaborate on documents and information to create operational efficiencies.
Implementing a system like this may seem overwhelming. One of the most difficult aspects can simply be determining how to get started. Starting small—with a single team or department—is often the best approach. Focusing on core SharePoint features, such as document management and lists, provides users with an easy to grasp introduction to the system. As comfort grows, SharePoint can then be expanded to support broader business processes and integrations with other Microsoft Power Platform® tools.
Benefits: Why do you need it?
SharePoint provides a simple, centralized solution for managing everyday business tasks using familiar technology. The platform gives users the opportunity to start small and build additional functionality and business efficiencies. For example:
- Document management in SharePoint allows businesses to store, organize, and collaborate on files in a secure and centralized environment.
- Lists function like spreadsheets or lightweight databases, ideal for tracking information, managing tasks, or logging activities.
Both of these features are “out of the box” functionalities of SharePoint that are easy to deploy and use, while delivering significant impacts to business efficiency and better control over business documents and data.
Technology Used
- SharePoint Site/Pages
- Document Libraries and Lists
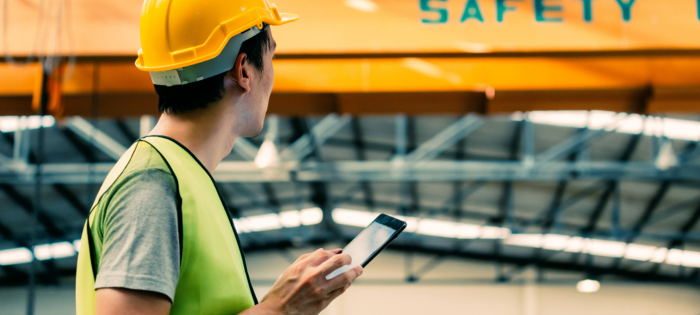
Tech Corner: Safety Inspection Form
Functionality: What does it do?
Management by walking around (MBWA), safety observations, and safety inspections are common terms for similar practices. All involve observing the daily work environment to assess safety practices. Historically, these types of observations have been completed using paper and pencil forms that typically get added to a binder and stored on a shelf—never to be reviewed again. KTL’s Safety Inspection Form provides an online tool for supervisors and/or employees to observe and document safety practices and/or inspect equipment and then use those observations to improve safety performance.
Benefits: Why do you need it?
KTL’s Safety Inspection Form offers the following:
- Provides a list of questions or items to inspect (e.g., equipment, safety procedures) to help ensure consistent and repeatable inspections.
- Creates an electronic means to conduct and document safety inspections.
- Collects data that can then be analyzed to identify common problems.
- Sends notifications, including alerts for negative findings and exceeding certain thresholds, as well as weekly summaries.
- Facilitates the company’s ability to provide recommended corrections to the employee being observed or to alert maintenance of necessary equipment repairs.
- Helps the company to focus resources on correcting common safety issues where return on investment (ROI) is greatest.
Technology Used
- SharePoint
- Power Apps
- Power Automate
- Power BI
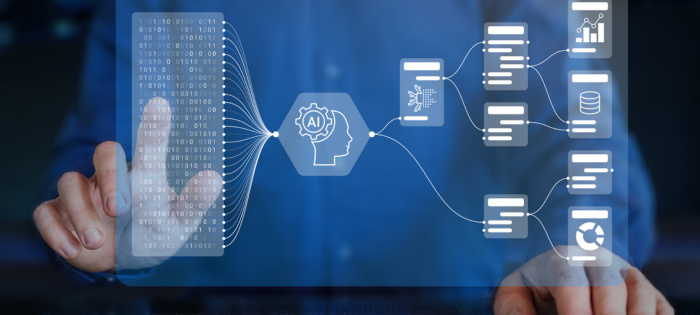
Tech Corner: Power Automate Tasks
Functionality: What does it do?
As part of Microsoft’s Power Platform®, Power Automate® is a workflow automation tool used to automate repetitive tasks and workflows. The purpose of workflow automation tools is to streamline manual processes and tasks in order to maximize company time and resources, increase operational efficiency, and improve overall business productivity.
Common Power Automate tasks include the following:
- Notifications: This can be as simple as creating a notification when something is submitted or changed or setting alerts to act according to a designated schedule (e.g., seven days before due date).
- Approvals: Documents and list items can be routed to specific individuals by email with a simple button to approve or decline and then automatically move along to the next step in the process.
- Document Management: Email attachments can be automatically added to OneDrive® or SharePoint; metadata (e.g., time/date, sender, and email body) can also be added.
- Form Processing: Form processing can automatically create ID numbers for list items to help with tracking. In addition, data from one form can be used to populate multiple lists. For example, entering data into a customer feedback form includes a checkbox asking if it requires a corrective and preventive action (CAPA). If so, relevant data from the feedback form populates a new entry in the CAPA list.
- Records Management: When a record is created, the retention period can be added. When the retention period expires, the record is then automatically archived or deleted.
- Calendar Management: With calendar management, you can do things like email yourself a list of your calendar entries daily or weekly, email reminders for any calendar entries you have not yet responded to, and create Outlook events or meetings from a Power App® button.
- Data Management: Large data sets can be transferred easily from Microsoft Excel® to SharePoint. Data can also be manipulated, cleaned, or transformed during or after the transfer.
Benefits: Why do you need it?
- Fewer mistakes. Replacing manual data entry with automation reduces opportunities for human error and the potential mistakes, inaccuracies, and costs that can accompany it.
- Streamlined processes. Workflow automation creates more efficiency by automatically making assignments and moving projects/documents/tasks along in the process. It is also easier to track and manage processes and performance when all steps are in Power Automate.
- Improved productivity. Automating manual tasks frees up time and resources to focus attention elsewhere. Being able to easily track a project or process through an automated system can further improve productivity and ensure tasks are completed as planned.
- Enhanced collaboration and accountability. A clearly designed workflow helps ensure all employees understand the process and their role in it. A common system further enables cross-functional collaboration and improves accountability.
- Informed business decisions. Power Automate offers real-time reporting and performance metrics that can be used to inform decisions and modify processes to enhance performance.
Technology Used
Microsoft Power Automate
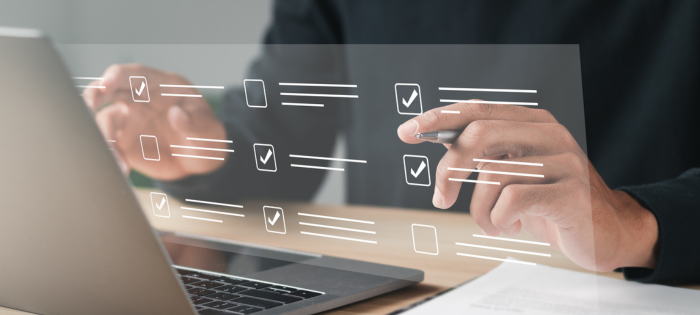
Tech Corner: Task Tracking Tool
Functionality: What does it do?
Organizations face endless numbers of tasks associated with compliance, certification, and other internal and external requirements. Task tracking can provide an effective project management tool to track all these tasks and their associated deadlines in one place. Leveraging Microsoft SharePoint®, KTL’s Task Tracking Tool not only tracks tasks to completion, it also allows project managers to assign tasks to responsible individuals, automate reminders, attach documents, share updates with their team, and more for any task—from project management to regulatory deadlines.
Benefits: Why do you need it?
KTL’s Task Tracking Tool offers the following benefits:
- Centralization: Users can view all tasks, owners, details, and due dates in one place.
- Customizable: All aspects of a task list can be customized to track the information you need.
- Notifications: Custom notifications can be tailored for upcoming deadlines, status changes, and task assignments.
- Recurring Tasks: Routine tasks can be scheduled to recur according to desired schedules.
- Dashboards and Reporting: Data related to tasks (e.g., percent completion) can be displayed visually to help identify and report on trends and patterns.
Technology Used
- SharePoint
- Power Automate
- Power Apps or alternative
- Power Bi
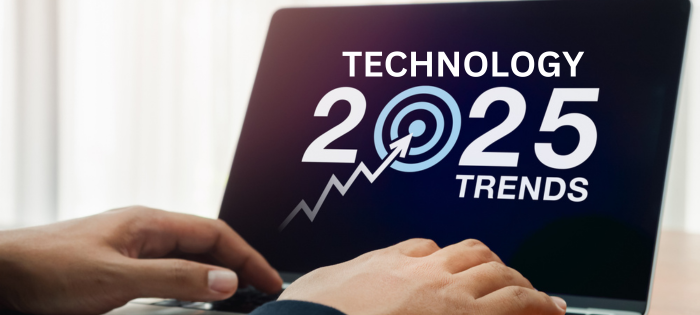
Technology: Top Trends for 2025
As the role of technology continues to expand at a significant pace, keeping up with advances can be challenging. Technology can offer opportunities to simplify compliance, create efficiencies, improve recordkeeping, inform better decision-making, and more if used appropriately. Here are some of the top Microsoft 365® technology advances KTL anticipates will be trends in 2025…
SharePoint® Modernization
SharePoint is constantly evolving to provide enhanced functionality to users. In 2016, Microsoft introduced the “modern” experience for SharePoint as a significant improvement, with its more modern interface that integrates better with mobile screens. When it was introduced, converting to the modern interface was optional; companies could continue operating their existing “classic” sites without necessitating significant updates. But in the past eight years, classic sites have become outdated, have limited mobile integration, and are beginning to experience performance issues resulting from limited ongoing support. Further, previous methods of creating custom forms (InfoPath) or workflows (SharePoint Designer) are slowly being phased out in favor of modern replacements, and Microsoft is removing SharePoint 2013 Workflow from existing tenants and fully retiring it in April 2026.
Because of this, organizations are being pushed to migrate from classic to modern SharePoint to keep their sites running and usable. Beyond responding to the slow depreciation of classic sites, modern SharePoint offers significant enhancements that improve user experience and overall site performance. Transitioning from a classic SharePoint site to a modern one is not considered a “simple” process, because there is no one-to-one mapping between the functionality offered by classic web parts and what is offered on modern pages. But it is worth doing. Modern sites are less costly to create, quicker to implement, easier to manage, and much simpler to edit and update.
Digital Forms
Companies have completed inspections and assessments via paper forms for years. Many still follow this traditional process, creating mountains of paperwork and related inefficiencies. Digital forms are a simple technological advancement that more companies are embracing to improve compliance and productivity. Digital forms allow employees to quickly and easily collect data from a mobile device—from daily inspections (e.g., forklifts) to near-miss information—as it is happening in the plant/field. That data is submitted directly to the system and can then be further analyzed through dashboards to identify concerns and trends. Notifications for identified issues and program compliance can also be configured to create greater visibility.
With digital forms:
- Data can be submitted directly and immediately for review with no manual data entry required.
- Data is stored for future analysis and improvements.
- Issues can be identified quickly and assigned to relevant people for resolution.
- Program compliance is tracked in real time.
Custom Business Apps
Power Apps is Microsoft’s low-code platform for creating custom business apps. Users can create apps, add their own data sources, create custom workflows, design their own user interface—all without extensive coding experience. With its growing popularity, Microsoft is continuing to expand Power Apps’ functionality and help more organizations leverage its flexibility. Specifically in 2025, Power Apps users can look forward to the following advances:
- Deeper integration with Microsoft 365 and other emerging technologies/data sources to create smoother workflows, better collaboration between tools, and an overall simpler user interface and experience.
- Enhanced low-code/no-code capabilities, such as more drag-and-drop features, visual interfaces, and templates to allow for faster development of line-of-business apps, mobile apps, and web apps.
- Improved mobile responsiveness to ensure Power Apps functions well not only on computers, but also on smartphones and tablets.
- Integration with Power BI to allow businesses to develop comprehensive data solutions, manage workflows, and visualize key metrics through dashboards (see below).
Automated Workflows
Microsoft Power Platform® allows businesses to automate workflows and streamline and standardize processes. For example, a document approval workflow can be set up to automatically route documents, assign review tasks, track progress, and send reminders and notifications when needed. It takes documents from development through final approval, ensuring documents are reviewed at the appropriate time by the appropriate party.
Automated workflows can be developed for virtually any business process, and the benefits of doing so are many, including:
- Standardized and streamlined approach for approving and completing tasks.
- Improved accuracy with less opportunity for human error.
- Business efficiencies from automated and streamlined practices.
- Version control and history to create a reliable audit trail.
- Improved access/security for sensitive information.
Data Visualization and Insights
A dashboard is a tool used to quickly display and visualize data, typically using charts, tables, and other graphic elements. Dashboards provide a quick and simplified way for users to understand complex data sets, review key performance indicators (KPIs), and identify trends or patterns.
The data collected in most business processes—ranging from the outputs of an inspection form to the inputs into a companywide sales program—can be displayed in a dashboard. Centralizing and visualizing this data can have significant business benefits, including the following:
- Dashboards provide an integrated view of data pulled from multiple sources into an easy-to-read display.
- Simplified data visualization allows for improved and more efficient decision-making.
- Dashboard metrics provide for monitoring of data that has been collected.
- The collaboration, customization, and transparency provided through dashboards help support organizational objectives.
Getting Ahead in 2025
Traditional processes tend to produce traditional results. Integrating technology can help companies to stretch and empower every limited resource. The key is identifying those traditional processes that will realize benefit from technological integration, such as those outlined above.
The right technology can enhance traditional business practices to create greater efficiencies and enhanced business value. Integrating technology with current business practices not only allows for continual improvement, it also helps create the next level of competitive advantage. Doing so requires businesses to start thinking strategically about these trends now. It also requires working with someone with the technology expertise to design and build scalable systems that allow the organization to more efficiently and effectively manage compliance and business processes. Technology solutions should be designed with the end in mind. That means considering the company’s immediate issues/needs within the context of the overall business need, and then formulating platforms/systems, as required, into an aligned system.
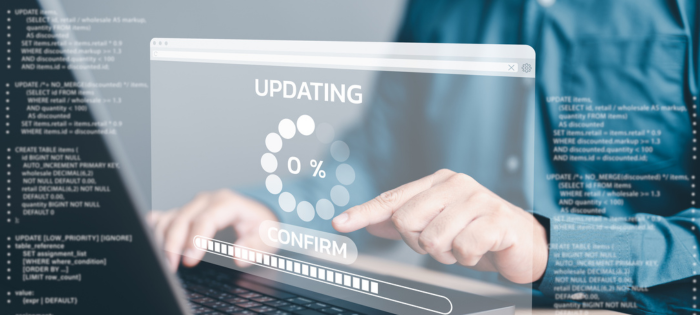
Tech Corner: SharePoint® Modernization
KTL uses the Microsoft Power Platform®—including SharePoint®—as a suite of dynamic information management tools that can be customized to provide streamlined, centralized information management and consolidated reporting to all levels of the organization.
SharePoint is constantly evolving to provide enhanced functionality to users. In 2016, Microsoft introduced the “modern” experience for SharePoint as a significant improvement, with its more modern interface that integrates better with mobile screens. When it was introduced, converting to the modern interface was optional; companies could continue operating their existing “classic” sites without necessitating significant updates. But in the past eight years, classic sites have become outdated, have limited mobile integration, and are beginning to experience performance issues resulting from limited ongoing support. Further, previous methods of creating custom forms (InfoPath) or workflows (SharePoint Designer) are slowly being phased out in favor of modern replacements. Because of this, organizations are being pushed to migrate from classic to modern SharePoint to keep their sites running and usable.
Benefits
Beyond responding to the slow depreciation of classic sites, modern SharePoint offers significant enhancements that improve user experience and overall site performance, including the following:
- Modern, Intuitive Interface: The user-friendly interface offers streamlined navigation, improved layouts, and mobile responsiveness for optimal viewing on different screen sizes (e.g., phone, laptop, desktop, tablet). This provides easier user interaction and enhanced accessibility in the office, plant, field, etc.
- Performance Optimization: Modern SharePoint sites are optimized for performance. The search functionality is more powerful and produces more relevant search results that are easier to filter and find. Optimization also creates faster page load times to improve efficiency for users.
- Flexible Modern Web Parts: Modern’s wide range of configurable web parts can be simply added or modified to update site content.
- Custom Workflows and Automation: Modern SharePoint can be more easily tailored to specific business needs by integrating Power Automate, Power Apps, and other apps to build custom workflows, forms, and automations that support changing business processes.
- Seamless Microsoft 365 Integration: Modern SharePoint integrates deeply with other Microsoft 365 tools, including Microsoft Teams, OneDrive, and Planner. This makes collaboration more efficient, as employees can work together in real-time using familiar tools.
Get Modernizing
Microsoft suggests taking a four-step approach to transitioning from a classic SharePoint site to a modern one:
- Assess. Inventory your existing site, determine priorities for modernization, and establish a clear scope of work.
- Strategize. Develop a strategy for how the classic site will be transformed into a modern site, considering the various impacts of the transition on different elements of your system.
- Execute. Create an implementation plan to outline what needs to happen to update each site and associated roles, responsibilities, tasks, and timelines.
- Enhance. Consider the many opportunities for integrations and enhancements to address business needs once sites have been converted.
Transitioning from a classic SharePoint site to a modern one is not considered a “simple” process, because there is no one-to-one mapping between the functionality offered by classic web parts and what is offered on modern pages. But it is worth doing. Modern sites are less costly to create, quicker to implement, easier to manage, and much simpler to edit and update.
If you currently have a classic SharePoint site, KTL can walk you through the modernization process to help ensure your sites deliver improved functionality, enhanced user experience, and better overall performance. Please reach out and set up a no-obligation demo.
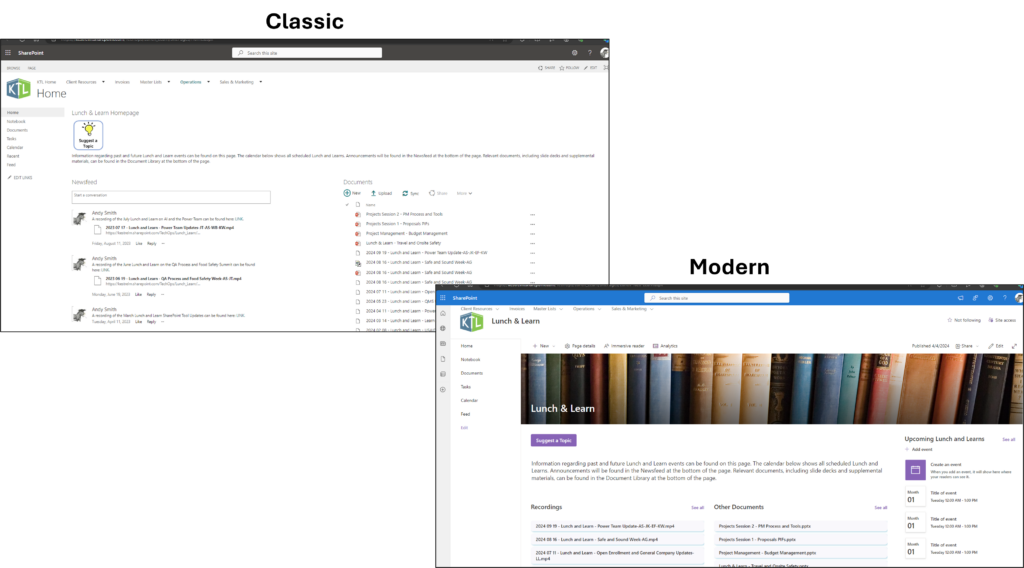
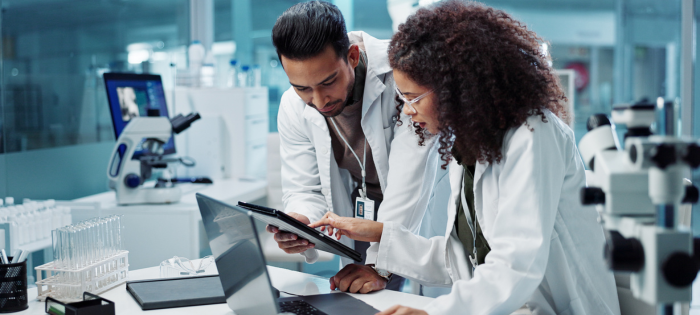
Tech Corner: Laboratory Information Management System
Functionality: What does it do?
Laboratory Information Management Systems (LIMS) are tools designed to manage laboratory samples, associated data, and workflows in a user-friendly interface. KTL uses the Microsoft Power Platform to build and customize LIMS to provide organization-specific functionality, including the following:
- Samples can be tracked as individual or grouped assays.
- Workflows can be established to improve processing and reduce errors.
- Data is centralized for access and quality control improvements.
Benefits: Why do you need it?
Having a reliable LIMS can help organizations to:
- Manage and control large amount of laboratory data and samples.
- Reduce time required to track samples.
- Create detailed chain of custody.
- Provide notifications and tracking of approvals.
- Attach documents and photos to samples to provide more detailed information.
- Deliver results to identified users.
Technology Used
- SharePoint or Dataverse
- Power Apps
- Power Automate
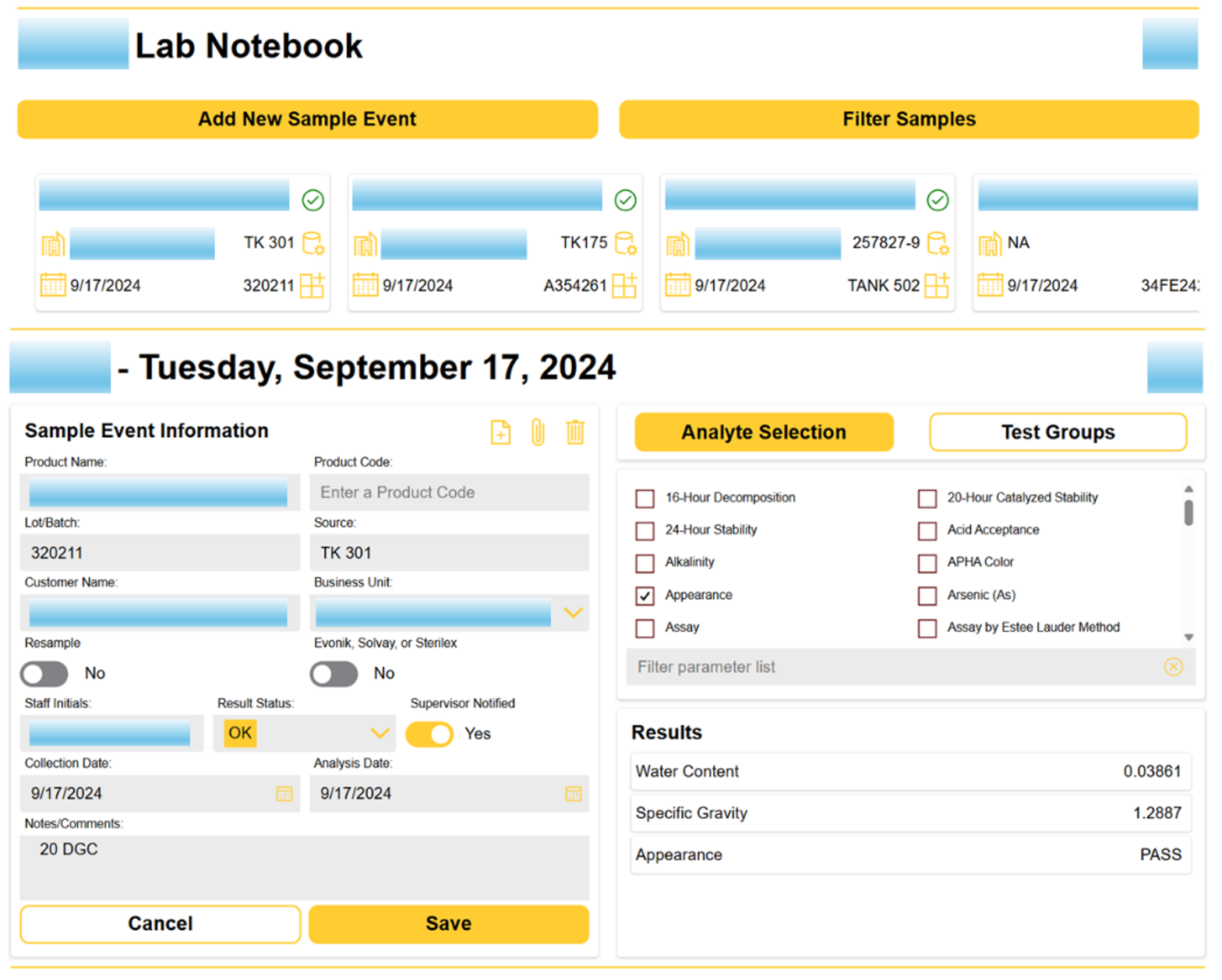
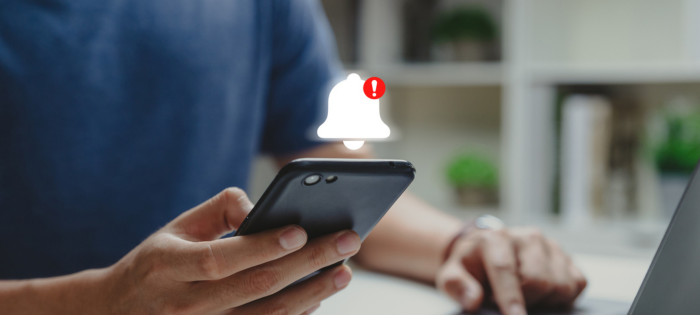
Tech Corner: Reminders and Notifications Tool
Functionality: What does it do?
Virtually every regulatory agency (e.g., EPA, OSHA, FDA, USDA) and voluntary certification standard (e.g., ISO, GFSI, organic) has compliance requirements that call for companies to fulfill compliance activities by established deadlines. KTL’s Reminders and Notifications Tool is designed to help organizations make sure these deadlines are not missed. The tool allows users to receive notifications and reminders via email, Microsoft Teams, or other messaging app that action is needed, including the following triggers:
- Document submissions
- Survey/list submissions
- Permit renewals
- Assignment due date is approaching/past due
- Item or document is awaiting approval
- Many, many others
Benefits: Why do you need it?
The Reminders and Notifications Tool helps organizations to:
- Keep multi-step processes moving forward quickly and efficiently.
- More efficiently manage compliance deadlines.
- Remind assigned staff of easy-to-forget due dates.
- Share information and reports with notifications to disseminate key information regularly.
Technology Used
- SharePoint
- Power Automate
- Email, MS Teams, or other communication platform