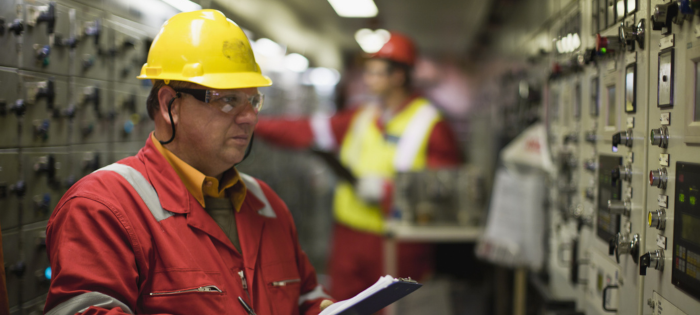
Comments: No Comments
OSHA Inspections: Site-Specific Targeting
The Occupational Safety and Health Administration (OSHA) uses inspections to help ensure employers provide safe and healthy workplaces. In April 1999, OSHA implemented its first nationwide Site-Specific Targeting (SST) plan to conduct comprehensive programmed inspections in non-construction worksites with 20 or more employees. The SST inspection program has been renewed and updated since that time, and on May 20, 2025, OSHA issued the most recent directive for its SST inspection program. This new version is more narrowly focused, prioritizing programmed inspections at establishments with high or upward-trending injury and illness rates, as well as those that failed to submit required information.
Key Changes
The SST program uses injury and illness data that employers submit under 29 CFR 1904.41 through OSHA Form 300A. The new SST directive was updated to rely on data from calendar year (CY) 2023 versus CY 2021, reflecting OSHA’s continued efforts to allocate enforcement resources based on the most recent injury and illness data. OSHA then uses this data to target and identify facilities for a potential SST inspection, as follows:
- High-rate establishments: Facilities with elevated Days Away, Restricted, or Transferred (DART) rates for CY 2023. Importantly, OSHA will set one DART rate of manufacturing and a different DART rate for non-manufacturing to provide for equal targeting from both groups.
- Upward-trending establishments: Facilities with rates at or above twice the private sector national average in CY 2022 that have continued to trend upward annually from CY 2021-2023.
- Low-rate establishments: Those with low DART rates. Low-rate facilities will be randomly selected for inspection to verify the reliability of Form 300A data.
- Non-responders: Facilities that failed to submit CY 2023 Form 300A data, as required. A random sample of non-responders will be inspected to discourage employers from not reporting.
What’s Involved
Based on data collected and the above criteria, OSHA Area Offices (AOs) select facilities to target for planned SST inspections. The SST inspections are comprehensive in scope and may be expanded with justification (e.g., including health hazards based on prior inspection history in industry classification).
During the SST inspection, the Certified Safety and Health Official (CSHO) will do the following:
- Review data. The CSHO will review available OSHA 300 Logs, Form 300A summaries, and 301 Incident Reports for CY 2021, 2022, and 2023.
- Conduct a facility walkthrough. During the walkthrough, the CSHO will evaluate potential hazards in all areas of the workplace; however, the focus will largely be on those areas where the facility has had documented injuries and illnesses.
- Evaluate employee exposures. The CSHO will pay particular attention to hazards observed during the walkthrough, discussed in employee interviews, and/or identified on OSHA 300 Logs and 301 Incident Reports.
- Assess the safety and health management system. The SST inspection will focus on whether the management system is adequate to identify and address the elevated injury and illness rates.
- Conduct a closing conference. The CSHO will discuss with the employer identified hazards, gaps in reporting practices, and deficiencies in the safety and health management system during the closing conference.
What You Can Do
The updated SST inspection program update reflects OSHA’s ongoing commitment to data-driven enforcement and targeted inspections in general industry. Correspondingly, accurate data is critical. Facilities must have their OSHA recordkeeping and reporting practices in check. Not only should records be verified as accurate and complete, but each accident should have a documented corrective action. This information should be checked, and any additional actions should be made to fully comply with Occupational Safety and Health (OSH) Act requirements.
But beyond recordkeeping and reporting, facilities can take steps to avoid an SST inspection altogether by making sure they have the processes, programs, and systems in place—and documented—to protect employees’ safety and health:
- Develop comprehensive safety programs and a robust safety management system. A compliance management information system can provide a centralized location to track and manage all safety-related information (e.g., policies, procedures, and practices) to not only help ensure going compliance but to also provide the documentation required should an inspection occur.
- Regularly assess the level of existing OSHA programs against compliance issues and potential accidents. Identify what may need to change in the facility’s OSHA compliance programs and practices to ensure their effectiveness and then implement and document appropriate corrective actions.
- Maintain robust occupational health and safety and incident. Information technology (IT) tools, such as KTL’s OSHA 300 Power App, with its comprehensive intake form tailored to OSHA 300 and OSHA 300A requirements, make it easier to collect, search, and analyze data—and maintain OSHA compliance. Using a digital forms further helps ensure no crucial data points are missed and makes it easy to filter, search, and analyze records and data to offer deeper insights into safety performance.
- Understand what to expect from an OSHA inspection. Educate staff on the process a CSHO will follow and make sure team members understand their roles in the inspection. Prepare staff to respond appropriately to the CSHO’s questions and, importantly, make sure they know how to locate requested documentation.
- Train employees. All employees should receive ongoing training to fully understand and follow safety processes and procedures. Training should focus on worker knowledge and understanding their responsibilities to comply with identified requirements.
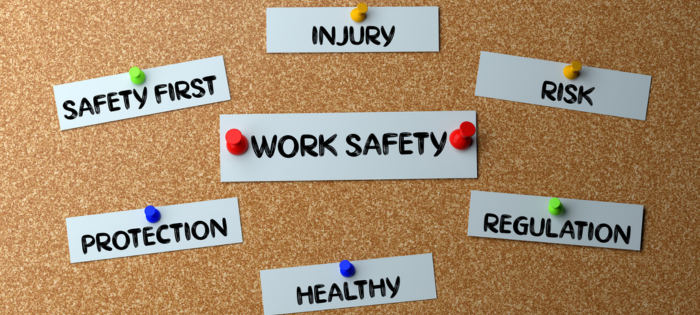
Comments: No Comments
5 Resolutions for Health and Safety
As discussed in KTL’s recent EHS: Top Trends for 2025 article, there are a number of anticipated challenges and opportunities in environmental, health, and safety (EHS) for 2025—some ongoing and some just gaining traction with impacts yet to be known, particularly with the change in Administration just taking hold. Regardless, the importance of investing in a strong health and safety program cannot be underestimated. Here are five tips to help start the year strong in health and safety.
1. Plan for Consistency. With so many changes happening in the world at such a rapid-fire pace, consistency creates a predictable environment for employees to maintain positive health and safety practices. Consistency in both action and communication is equally important in the health and safety world. Inconsistent expectations and actions lead to inconsistent behaviors. Ambiguity in messaging and instructions can further cause health and safety hazards.
Keep it simple and consistently reinforce the same message to elicit consistent safety performance. As some examples:
- Always use the right tool for the job.
- Stop work when needed to address hazards.
- Communicate with other personnel about hazards.
- Always wear the proper personal protective equipment (PPE) for each task.
2. Focus on Continuous Small Improvements. Continuous improvement does not mean erratic change. Change should be sustainable, and that happens best when it is introduced and implemented incrementally. Small changes can lead to big differences; it just requires a plan. Identify the big goal, and then define those small steps needed to reach it. Thinking big but acting small can help create buy-in across the organization, consume fewer resources, and create small “wins” more quickly to drive momentum toward reaching the big goal.
3. Prioritize Communication in All Forms. When it comes to the characteristics of an excellent safety culture, communication is at the top. It is vital that all levels of management (i.e., senior, middle, supervisory) communicate their commitment to safety clearly to workers. It is equally important that workers feel empowered to discuss their safety concerns. Having a safety culture where workers do not feel like they can speak up at work when it comes to their safety can present significant threats to workers and the overall well-being of the company.
- Use a variety of communication channels (e.g., one-on-one conversations, regular safety briefings, written materials, visual aids) to improve worker understanding.
- Practice active listening; communication goes two ways!
- Be clear, concise, and consistent in your messaging (see #1 above).
4. Incorporate Leadership. In its Recommended Practices for Safety and Health Programs, the Occupational Safety and Health Administration (OSHA) outlines best practices for implementing and maintaining a health and safety program. Management leadership is a core element. According to the guide, management provides the leadership, vision, and resources needed to implement an effective health and safety program. Management can exhibit this in several ways:
- Demonstrate a commitment to continuously improving workplace health and safety, including eliminating hazards and protecting workers.
- Make safety and health a core organizational value with associated health and safety goals and objectives.
- Establish program expectations and responsibilities that engage employees.
- Provide adequate resources and support for the program
- Set a good example when it comes to prioritizing health and safety.
- Communicate regularly with workers about the importance of workplace health and safety.
5. Encourage Worker Participation. Worker participation is another of OSHA’s core elements of workplace health and safety in its Recommended Practices for Safety and Health Programs. Engaging workers at all levels in establishing, implementing, evaluating, and improving health and safety in the workplace creates buy-in. It is important that organizations encourage workers to report health and safety concerns and promote a psychologically safe environment. Organizations should also work to actively engage employees in other health and safety initiatives, such as conducting hazard assessments, developing policies, serving on safety committees, leading toolbox talks, and more.
All of these tips come down to one thing—protecting employee health and safety. Regardless of external factors (e.g., regulatory uncertainty, supplier requirements, consumer demands, financial incentives, etc.), protecting employees should always be a top priority, and these five tips can help ensure you start the year strong.
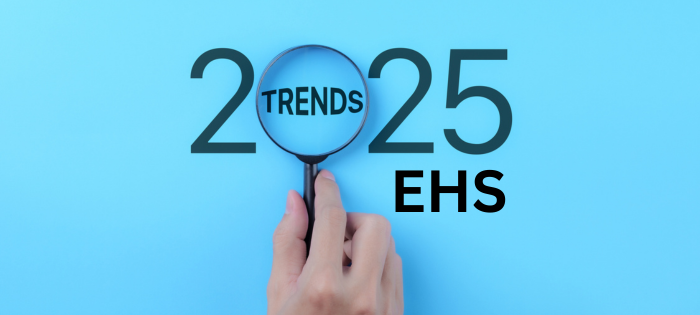
Comments: No Comments
EHS: Top Trends for 2025
Every year, we see a number of environmental, health, and safety (EHS) trends rise to the surface that have the potential to impact many industries. As we enter 2025, some challenges and opportunities in EHS remain ongoing; some are just gaining traction with impacts yet to be known, particularly with a change in Administration just taking hold. Here are some of the top EHS trends KTL is keeping watch on in 2025…
Regulatory Landscape
In 2022, the Environmental Protection Agency (EPA) published its FY 2022-2026 EPA Strategic Plan to communicate the Agency’s vision, priorities, and strategies. Specifically, the Plan includes targeted objectives and outcomes in the areas of climate change; environmental justice; compliance enforcement; clean land, air, and water; and chemical safety. The Occupational Safety and Health Administration’s (OSHA’s) focus centers on National Emphasis Programs (NEPs) for 2025 related to combustible dust, fall protection/prevention, heat, silica crystalline, and warehousing and distribution center operations, as well as many regional directives.
With a new Administration taking office in January, a big unknown of the coming four years is how the EHS regulatory landscape will change. There is speculation regarding plans to reorganize the EPA and establish “pause and review” teams to assess major rules, guidance materials, grants, legal settlements, budgets, etc. How this will translate into regulatory action remains to be seen.
Update: According to InsideEPA.com, acting EPA Administrator James Payne issued a directive on January 24, 2025, ordering all EPA staff to stop all communications with external parties pending further instruction. Exemptions will allow EPA staff to continue to communicate with state and federal agencies, provided they do not discuss enforcement matters; talk to relevant partieis to facilitate imports; and continue conducting inspections. It is unclear at this time how long the directive will remain in place.
Mental Health
Companies are increasingly recognizing that traditional safety programs must evolve to prioritize mental health as much as physical health—from mental health days to employee assistance programs, to stress management training, to flexible work hours. Correspondingly, psychological safety is becoming a critical concept for building effective teams and encouraging workplace innovation and success. A psychologically safe culture allows employees to take reasonable risks in a safe environment without negative interpersonal consequences.
A related concept is safety culture, which is concerned with many cognitive aspects of safety, like norms, perceptions, beliefs, and values. Emphasizing mental health as part of the organization’s safety culture may become a priority for mature organizations. As the concept of total worker health continues to expand, the focus on mental health is also likely to be reinforced by new regulations and standards regarding psychological safety in the workplace.
Sustainability and Climate Change
Environmental, Social, and Governance (ESG) initiatives have dominated many corporate agendas for the past several years, particularly with Europe and Canada advancing standards related to sustainability and climate change data reporting and ISO’s recent Climate Change Amendments. Many organizations have worked to significantly improve their data collection efforts and have integrated climate change management and circular economy principles into their sustainability strategies.
The change in Administration may increase scrutiny regarding the value of these ESG initiatives. We have already seen the Securities and Exchange Commission’s (SEC) March 2024 Climate-Related Disclosures Rule stayed due to multiple petitions and lawsuits. This may be a sign of things to come. Many companies have invested in their ESG efforts and will continue to do so, but 2025 may present an opportunity to reassess and streamline initiatives to ensure they are practical and upholding sustainability goals, while also contributing value to the company.
PFAS
Per- and polyfluoroalkyl substances (PFAS) became a focal point for EPA in 2021 with the publication of its PFAS Strategic Roadmap, which committed to addressing concerns related to PFAS exposure. Actions have included improving reporting on PFAS, as well as adding seven additional PFAS to the Toxics Release Inventory (TRI) in January 2024 and an additional nine in January 2025. In April 2024, EPA announced three more notable actions, including introducing the first-ever national drinking water standards and designating perfluorooctanoic acid (PFOA) and perfluorooctane sulfonic acid (PFOS) as “hazardous substances” under Superfund. In addition, the updated Interim Guidance on the Destruction and Disposal of PFAS and Materials Containing PFAS will require entities to report releases of these “forever pollutants” that exceed threshold quantities.
Beyond federal regulations, many states are introducing policies related to PFAS, including monitoring and testing for PFAS in water and sewage sludge and banning PFAS in food packaging, clothing, and other consumer products. Organizations need to address PFAS in their operations, products, supply chains, and waste streams; stay informed about ongoing PFAS regulatory developments; and adjust compliance programs and operational practices, as needed.
Personal Protective Equipment (PPE)
Properly fitting PPE is essential for workers to complete their tasks safely. If PPE is not correctly fitted to the body, it can cause discomfort and increase the risk of workplace accidents and injuries. On December 11, 2024, the Occupational Safety and Health Administration (OSHA) announced its finalized revision to the PPE Standard for Construction, which requires PPE to properly fit any construction worker who needs it, including women and physically smaller or larger workers.
Employers must ensure that every employee not only has the right PPE, but that it also fits. Fit testing may identify the need for PPE alternatives to meet the anthropometric needs of all workers. Importantly, employees must be trained and empowered to speak up if PPE does not fit appropriately to ensure their safety.
Technology/AI
Artificial intelligence (AI) and machine learning technologies have the capacity to significantly alter how companies manage their EHS programs. While still not fully mature, these technologies are becoming more sophisticated. As AI evolves and becomes more generally accepted, more companies are likely to start adopting it to automate routine compliance tasks, conduct EHS assessments, perform training simulations, predict potential safety incidents, monitor workplace conditions in real-time, and more.
While the efficiencies and other benefits of technology solutions are many, the increased reliance on AI and machine learning will require increased oversight and management. In particular, companies will need to determine where automation is appropriate and where the human factor is still required. Not all processes lend themselves to AI. It will also be imperative to consider stronger data privacy protocols to ensure the security of the company.
Others to Watch
- OSHA Reporting: On January 1, 2024, the Department of Labor’s (DOL’s) final rule requiring employers in designated high-hazard industries to electronically submit injury and illness information to OSHA took effect. KTL inspections routinely find errors and omissions in OSHA recordkeeping. Effective solutions, particularly areas where hard copies can be replaced by digital forms, are needed.
- Hazard Communication Standard: The final Hazard Communication Standard took effect on July 19, 2024, implementing the first major updates since 2012. The first compliance date requires chemical manufacturers, importers, and distributors to update labels and Safety Data Sheets (SDSs) for chemical substances by July 19, 2026.
- Lead Levels: In January 2024, the EPA reduced the acceptable amount of lead in soil for residential exposure, stating that no level of lead is acceptable. These reduced levels may soon be translated into commercial exposures.
- One Health: Both the Society of Environmental Toxicology and Chemistry (SETAC) and Society of Toxicology (SOT) have adopted One Health initiatives as an integrated, unifying approach that aims to sustainably balance and optimize the health of people, animals, and ecosystems (SOT). The idea is to look at the health of our environment and all aspects of our environment as a whole and not one component at a time. This idea is being translated into health impact assessments.
- Pesticide/Herbicide Re-evaluation: The EPA has initiated re-evaluations of registered pesticides, herbicides, rodenticides, and fungicides, including the highly publicized Roundup. These reviews are expected to result in a recommendation to focus the use of these chemicals rather than using a general broadcast application.
- Microplastics: Microplastics have been found in every ecosystem on the planet—in food, beverages, and human and animal tissue. Scientists do not fully understand the impacts of microplastics on human health and aquatic life, and industry is struggling with how to manage them due to their pervasive nature and wide variety of shapes and sizes. Ongoing research in pollution prevention will be forthcoming.
Getting Ahead in 2025
In 2025, organizations will continue to encounter evolving workplace challenges, regulatory adjustments, societal demands, economic pressures, and rapid advancements in technology—some of which can be anticipated, some which remain to be seen. KTL suggests completing the following early in 2025 to prepare for whatever is on the horizon:
- Get senior leadership commitment. Even with the best EHS personnel, the organization and its EHS system will only be as strong as the top leadership and what they prioritize.
- Stay abreast of regulatory developments. Monitor what is going on at the federal (i.e., EPA and OSHA) and state levels, assess your regulatory applicability, and evaluate how any potential regulatory changes over the next year(s) may impact your operations.
- Conduct a comprehensive gap assessment to ensure you are efficiently meeting your EHS requirements (i.e., regulatory, management systems, internal, supply chain). Think critically about how overlapping requirements may apply (e.g., your chemical inventory may uncover requirements for air permitting, waste management, Tier II report, etc.) and how you can integrate systems to improve efficiency and compliance.
- Determine where you can integrate technology solutions into your operations. This could mean stepping into the world of AI and machine learning; it could also mean implementing compliance information management systems to help manage compliance and reporting requirements. Technology advancements can help create significant business efficiencies when used appropriately.
- Seek third-party oversight. Many EHS departments are severely understaffed. Having external experts periodically look inside your company provides an objective view of operations, helps you to prepare for audits, and allows you to implement corrective/preventive actions that ensure compliance. An outside expert can often provide the “big picture” view of what you have vs. what you need; how your plans, programs, and requirements intersect; and how you can best comply with changing requirements.
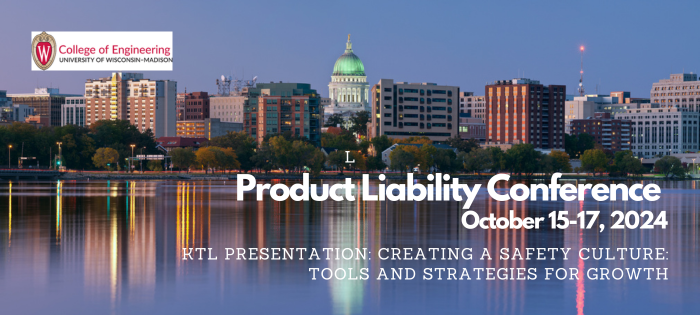
Kestrel Tellevate News / Safety
Comments: No Comments
KTL to Present on Tools to Create a Safety Culture
Look for KTL October 15-17, 2024 at UW-Madison’s 36th Annual Product Liability Conference in Madison, WI. The Conference presents current and emerging product liability prevention practices. KTL will be leading the following session as part of the Conference agenda:
Creating a Safety Culture: Tools and Strategies for Growth
Session 6 | Presenters: Will Brokaw, MS, Consultant, and April Greene, CSP, CHMM, Consultant
Safety culture is the sum total of your organization’s values, beliefs, attitudes, and actions toward safety. It is often referred to as “the way we do things around here” regarding safety. Previous research has identified key attributes or qualities that positive safety cultures share. This presentation will review these key attributes, provide real world examples, and discuss tools and strategies organizations can use to assess and improve their existing safety culture.
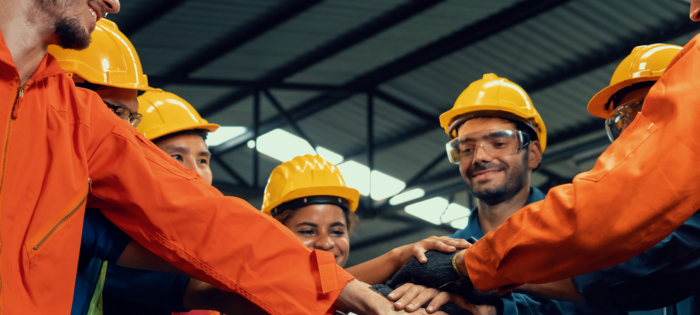
Comments: No Comments
Effective Safety Leadership
Safety Focus
A strong safety culture has several characteristics in common. KTL’s research into the topic of safety culture has identified two traits that are particularly important to an effective safety culture: leadership and employee engagement. Best-in-class safety cultures have robust systems in place to ensure that each of these traits, among others, is mature, well-functioning, and fully ingrained into the standard practices of the organization.
Best Practices: Management Leadership
In its Recommended Practices for Safety and Health Programs, the Occupational Safety and Health Administration (OSHA) outlines best practices for implementing and maintaining a safety and health program. Management leadership is a core element. According to the guide, management provides the leadership, vision, and resources needed to implement an effective safety and health program. Management can exhibit this in several ways:
- Demonstrating a commitment to continuously improving workplace safety and health, including eliminating hazards and protecting workers.
- Making safety and health a core organizational value with associated safety and health goals and objectives.
- Establishing program expectations and responsibilities that engage employees.
- Providing adequate resources and support for the program
- Setting a good example when it comes to prioritizing safety and health.
- Communicating regularly with workers about the importance of workplace safety and health.
OSHA’s guide outlines four action items for management to “walk the talk” when it comes to safety and health:
- Communicate your commitment to safety and health. Management should develop a clear, written policy that demonstrates safety and health is an organizational priority. The policy should be communicated to all workers and other relevant parties, be visible in the workplace, and be reinforced by management when operating the business.
- Define program goals. These goals should focus on specific actions to improve workplace safety and health. Goals should be accompanied by assignments and timeframes to help ensure they are achieved.
- Allocate resources. Resources may include employee time, supplies, training, tools, access to safety and health experts, funds, etc. Management should integrate safety and health into the planning and budgeting process to ensure resource needs can be met.
- Expect performance. Employees need to be engaged to perform. Establish responsibilities, provide encouragement, recognize accomplishments, and set up channels for employees to speak freely about safety and health issues.
Characteristics of Strong Safety Leaders
To be a great safety leader, management must regularly demonstrate the value of safety. Strong safety leaders demonstrate the following characteristics:
- Caring. First and foremost, safety leaders care deeply about their people. Caring is about doing whatever is necessary to ensure employees return home safely every night. It involves showing concern for the personal safety of individuals, not just making a commitment to the overall idea of safety.
- Vision. Senior management sets the strategic goals and vision for the company’s safety program. Strong leaders can visualize what safety excellence looks like, how to achieve it, and how to communicate about it.
- Commitment and Action. When it comes to safety, actions truly speak louder than words. A lack of commitment, as demonstrated by action (or lack thereof), comes across loud and clear to staff. For example, requiring staff to work excessive hours or use defective parts to meet productivity goals sends a clear message that productivity is more important than safety.
- Communication. Safety leaders not only communicate the strategy clearly to the workers who carry out the company’s mission, they also incorporate safety into regular communications and engage workers in discussions about safety and health.
- Collaboration and Cooperation. Safety works best if management and workers are on the same team. Cooperation means working together to develop a strong safety program (e.g., management involving line workers in creating safety policies and procedures). It means management seeks feedback from workers about safety issues—and uses that feedback to make improvements.
- Recognition and Accountability. Effective leaders will foster the sense that every person is responsible for safety throughout the organization. They use recognition to positively reinforce safe behaviors vs. blame when incidents occur.
- Credibility and Trust. Trust in the safety program and in each other is built when leaders demonstrate these characteristics and safety is treated as a company-wide priority.
Strong safety performance is a cornerstone of any business. Management plays a key role in establishing a modeling a best-in-class safety culture where people want to work safely. These cultures can lead to:
- Fewer accidents, losses, and disruptions.
- Improved employee morale.
- Increased productivity.
- Lower workers compensation and insurance claims.
- Improved compliance with OSHA regulations.
- Improved reputation to attract new customers and employees and retain existing ones.
- Better brand and shareholder value.
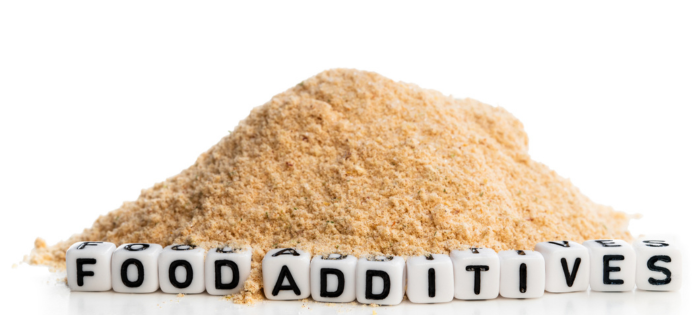
Comments: No Comments
Food Chemical Safety
Safety Focus
Food chemical safety is an area that is becoming a growing public concern, especially with states including California, Illinois, and New York challenging the safety of certain food additives and other chemicals used in food. Is food safe to eat if it has chemicals?
Chemical Presence in Food
The truth is…all our food is made up of chemicals. Some naturally exist in whole foods and provide nutrition. For example, the potassium in bananas is a chemical. Some chemicals, like environmental contaminants, get into food when crops absorb them from soil, water, or air. Process contaminants (e.g., undesired chemical byproducts) can also form during food processing, particularly when heating, drying, or fermenting foods.
Chemicals may also be added to food for a variety of reasons:
- Create additional nutritional benefits (e.g., vitamins A and D being added to milk).
- Provide protection from pathogens that could make people sick.
- Enhance food by adding flavor, improving texture, and changing appearance.
- Preserve quality by preventing spoilage or extending shelf life.
FDA Authorization
The Food and Drug Administration (FDA) must authorize any chemical added to food for use as a food or color additive before it may be used, unless the substance is generally recognized as safe (GRAS). Through its pre-market review programs, FDA reviews all relevant information about the chemical before providing its authorization, including information about:
- The identity of the chemical, including its chemical structure and data on other similar substances.
- How the substance will be used, its level of use, and the amount people may be exposed to in food.
- Toxicology, safety data, and other information to show the substance is safe at calculated exposure levels.
How Much Is Too Much?
The presence of a chemical does not determine whether a food is safe to eat. Rather, it is the amount that counts.
FDA scientifically assesses the safe amount of a chemical in food by comparing how much chemical is in the food and how much someone is likely to consume daily with other safety data to determine whether a food is safe to eat. Any chemical has the potential to be harmful at a certain level, which is why this multi-pronged evaluation and extensive calculations are important.
FDA determines an Acceptable Daily Intake level for the chemical. This level has a “built-in” safety margin to ensure the allowable daily amount is actually much lower than the level known to have a possible adverse health effect.
When Food Chemicals Become Unsafe
Authorized chemicals normally used in foods as additives and preservatives can become hazardous when they are unintentionally added or are present beyond the established limits. When this happens, it can cause immediate illness and/or long-term health effects on consumers. FDA monitors the food supply for chemical contaminants and takes action when the level of a contaminant causes a food to be unsafe. Situations such as this result in food safety alerts, recalls, and withdrawals from the market.
FDA helps safeguard the food supply by evaluating the use of chemicals as food ingredients and substances that come into contact with food (e.g., packaging, storing, handling). But ultimately, food manufacturers are responsible for marketing safe foods and ensuring that they meet FDA requirements. The manufacturers are required to implement preventive controls to significantly minimize or prevent exposure to chemicals in foods that may be hazardous to human health.
More information can be found on food chemical safety at the following websites:
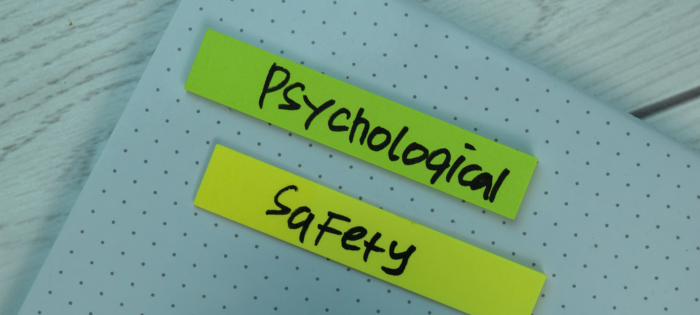
Comments: No Comments
Building Psychological Safety
Safety Focus
Workplace safety and health goes beyond the physical. A strong safety culture focuses on the whole person—and that includes ensuring psychological safety.
What is psychological safety?
Psychological safety is the shared belief that it is okay to take risks, express concerns and ideas, ask questions, speak up, and admit mistakes in the workplace without fear of being punished or humiliated. According to Amy Edmondson, PhD, Professor at the Harvard Business School, psychological safety is “felt permission for candor.” It allows employees the freedom to brainstorm, challenge the status quo, share feedback, take calculated risks, be vulnerable, and work through disagreements together.
Psychological safety brings in four different dimensions:
- Willingness to help: Employees are comfortable asking for help and trust that their colleagues are willing to provide it.
- Inclusion and diversity: Employees feel included and like their diverse experiences are accepted and valued.
- Attitude to risk and failure: Employees view mistakes as opportunities to learn and grow versus failures to be punished.
- Open conversation: Employees perceive conversations as open and candid; they feel safe speaking up and contributing to discussions.
Psychological safety develops over time. As organizations build greater psychological safety, they move through the following stages:
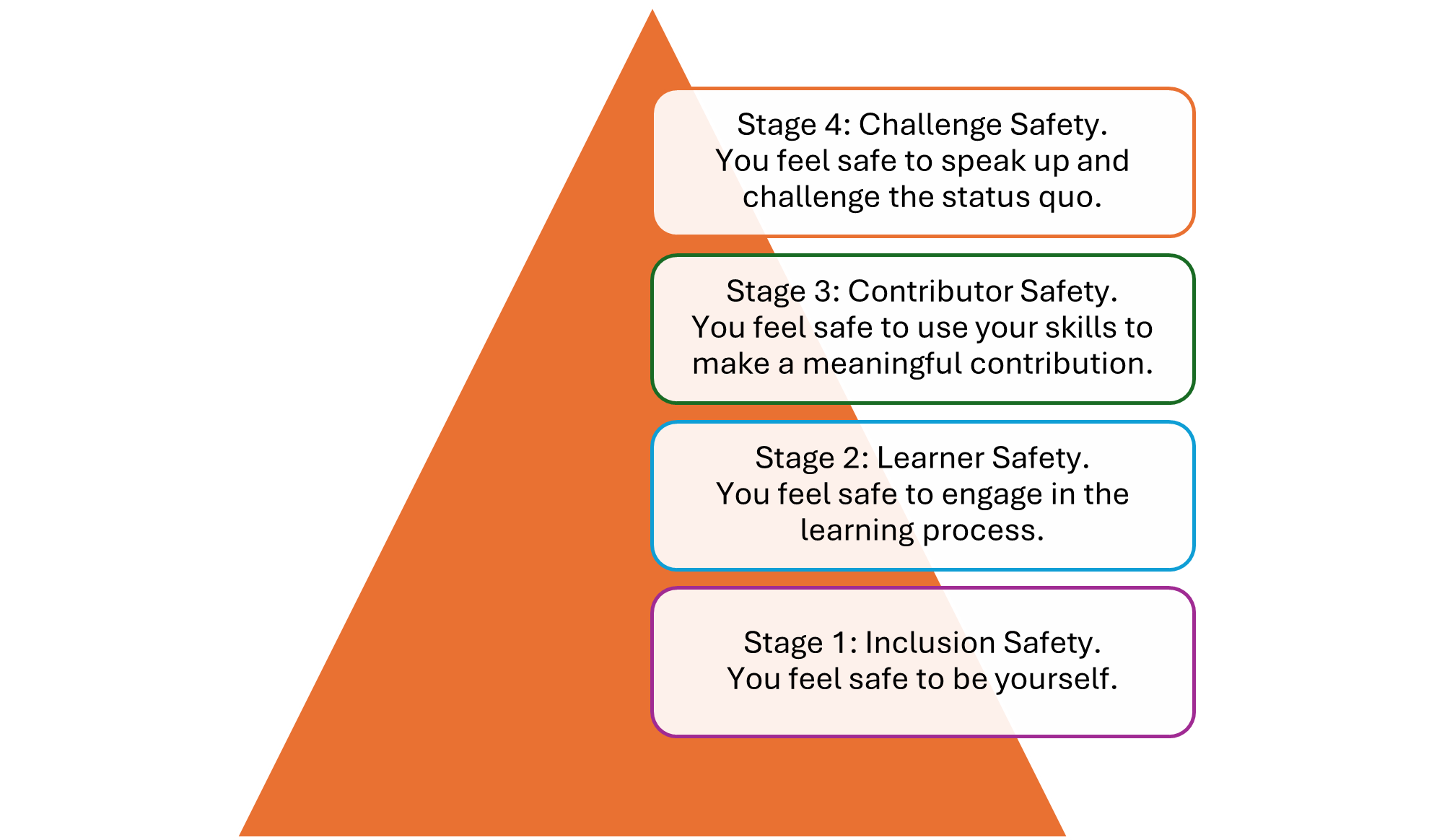
Why is psychological safety important?
Psychological safety is a critical concept for building effective teams and, many would argue, a critical concept for encouraging workplace innovation and success. According to the Center for Creative Leadership research, teams with high degrees of psychological safety report higher levels of performance and lower levels of interpersonal conflict. This is because employees who feel their workplace is psychologically safe are more willing to engage in behaviors that contribute to greater organizational innovation, including:
- Taking appropriate, thoughtful risks.
- Admitting, discussing, and learning mistakes.
- Openly confronting concerns and tough issues.
- Seeking help and feedback from others.
- Trusting other team members and believing they are there to support them.
- Trusting that they are a valued member of the team whose voice matters.
As psychological safety matures in a workplace, the benefits become more prevalent:
- More engaged team members. When employees can speak up without fear of retribution and feel like their contributions matter, they become more motivated.
- Better and more innovative decision-making. Diverse people voicing their opinions and concerns leads to more diverse perspectives being considered, providing the opportunity for innovation and more informed decision-making.
- A culture of continuous learning and improvement. Teams and individuals grow by sharing mistakes and turning them into opportunities to learn and make changes.
When an organization does not embrace psychological safety, there can be negative impacts on the overall performance of the organization and employee well-being, including stress, burnout, and turnover.
How do I create a psychologically safe workplace?
According to Edmondson, “Leaders must prioritize a culture of learning and innovation for team members to be comfortable speaking up, taking risks, and sharing information…It emerges with effort and curiosity and care.”
A lot goes into creating a psychologically safe environment—and building this culture takes time, focused attention, and good management practices, including the following:
- Make psychological safety a priority. Talk openly with your team about the importance of creating a psychologically safe workplace. Answer questions, dispel misconceptions, explain benefits, and connect it to the higher purpose of the organization innovation.
- Model the behaviors you want to see. Lead by example. Show how to raise concerns and tough issues in a constructive manner. Admit your own mistakes so others feel free to do so; normalize vulnerability.
- Facilitate everyone speaking up. Show genuine curiosity, be open-minded, encourage honesty, and actively listen when someone is willing to challenge the status quo. Make an intentional effort to promote dialogue by asking open-ended questions to get people to feel comfortable speaking up.
- Establish norms for how mistakes are handled. Use mistakes as opportunities for growth; encourage learning from failure by building lessons learned into every project. Do not punish mistakes, experimentation, and reasonable risk-taking.
- Be supportive. Show you are willing to explore out-of-the-box ideas. Embrace productive conflict. Promote constructive debate. Work to resolve conflicts productively. Employ a zero-tolerance policy for any employee deliberately undermining the efforts of another employee.
- Celebrate wins. Acknowledge what is going well, share credit, applaud people’s efforts, and appreciate thoughtful risk-taking. Publicly recognizing and celebrating the unique skills/talents of each team member will build trust and mutual respect.
- Continually reassess. It requires ongoing work and effort to keep your organization psychologically safe. Solicit feedback and track whether you are achieving the results you want.
How do I assess my workplace’s psychological safety?
Edmondson has created a seven-question survey that can be administered anonymously to measure your workplace’s psychological security:
- If you make a mistake on this team, will it be held against you?
- Are the members of this team able to bring up problems and tough issues?
- Do members on this team sometimes reject other members for being different?
- Is it safe to take a risk on this team?
- Is it difficult to ask other members of this team for help?
- Would anyone on the team deliberately act in a way that undermines efforts?
- Working with members of this team, are unique skills and talents valued and utilized?
Psychological safety is not about being nice. Many polite workplaces are not considered psychologically safe, because there is no opportunity for candor and people feel silenced by politeness. It is also not about feeling comfortable all the time. Yes, employees should feel comfortable speaking up, but pointing out mistakes, expressing concerns, and sharing opinions can feel very uncomfortable. Being vulnerable feels risky to most. A psychologically safe culture allows employees to take these risks in a safe environment without negative interpersonal consequences.
More information can be found on psychological safety at the following websites:
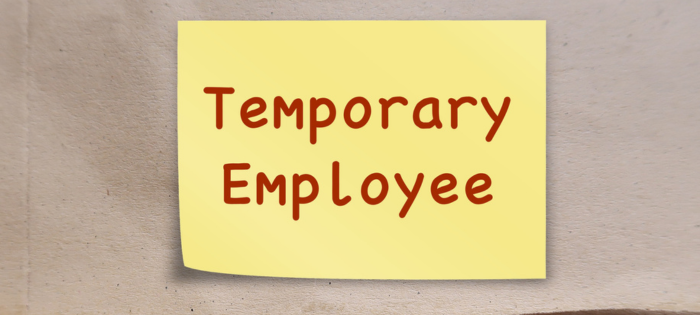
Comments: No Comments
Protecting Temporary Workers
Safety Focus
According to the American Staffing Association, America’s staffing companies hire approximately 16 million temporary and contract workers per year. These temporary workers are being more highly utilized than ever before, performing light and heavy industrial labor and other jobs with more complexity and, subsequently, greater health and safety risks. Temporary workers can add value to many businesses; however, using temporary workers should not be considered a cheap or easy fix.
Rights and Responsibilities
Temporary workers are those workers who are supplied to a host employer and paid by a staffing agency. The host employer and staffing agency are joint employers, which means both are responsible for providing and maintaining a safe working environment for temporary workers.
Under the Occupational Safety and Health (OSH) Act, all workers—including temporary employees—have the right to a safe and healthy workplace. To further protect temporary workers, the Occupational Safety and Health Administration (OSHA) launched the Temporary Worker Initiative in 2013, which focuses on ensuring compliance with the OSH Act. The Initiative addresses some common risks associated with joint employment and offers resources in plain language on topics such as health and safety training, recordkeeping, personal protective equipment (PPE), and hazardous communication.
Best Practices
Because temporary workers are jointly employed, the host employer and staffing agency have different health and safety responsibilities, some of which overlap. When hiring temporary workers, effective communication and understanding of responsibilities is vital to ensure workers are adequately protected.
The National Institute for Occupational Safety and Health (NIOSH) and the National Occupational Research Agenda (NORA) Services Sector Council—in partnership the American Society of Safety Professionals (ASSP), the American Staffing Association (ASA), and the Safety and Health Assessment and Research for Prevention (SHARP) program—published Protecting Temporary Workers: Best Practices for Host Employers as a guide to help staffing agencies and host employers better protect the health and safety of temporary workers.
The best practices are organized into the following three sections, each with a checklist to help guide the host employer in its health and safety efforts:
- Evaluation and contracting. Before commencing employment, the staffing agency and host must evaluate all facets of safety and health for the job(s) temporary workers are hired to perform. This includes reviewing all worksites, conducting a joint risk assessment, performing a job hazard analyses, and identifying any necessary training and protection required. Staffing agencies need to be aware of what conditions exist at the worksite, potential hazards that may be present, and how to ensure workers’ protection. This should all be specified in a written contract along with job details, communication responsibilities, injury and illness reporting responsibilities, and other aspects of workplace health and safety. Host employers should also include the staffing agency and temporary employees in any routine supplier or vendor evaluations of performance to minimize liability risks.
- Training for temporary workers and their worksite supervisors. Training is paramount. OSHA requires site- and task-specific safety and health training on approved tasks, hazard identification and control, PPE, OSHA laws/rights, emergency procedures, reporting health and safety concerns/incidents, accessing secure sites, safety and health program participation, etc. Generally speaking, providing this training is a shared responsibility. Staffing agencies conduct general safety and health training that is applicable to different occupational settings; the host provides site-specific training tailored to the hazards and conditions of the workplace. Supervisors should also be trained on approved tasks for temporary workers, process for changing job tasks, mentoring and supervision, OSHA laws, communication and reporting, and joint responsibilities of the host and agency. It is important to make sure supervisors are updated on any changes in temporary worker’s approved tasks and that they understand their responsibility and authority to correct any actions or behaviors that are unsafe.
- Injury and illness reporting, response, and recordkeeping. There should be a procedure for sharing illness and injury information between the joint employers. The host must also set up a method for employees to report work-related injuries and illnesses. If a temporary worker experiences and injury or illness, the host must inform the staffing company of the injury/illness, report it to OSHA, complete required recordkeeping (i.e., OSHA 300 log), conduct a joint investigation with the staffing agency, and coordinate medical treatment/return to work. The host should also have a program to reduce the number and severity of workplace injuries and illnesses and ensure that temporary workers are trained and participate in it.
Research indicates that temporary workers may be more at risk of work-related injury than permanent employees. As temporary workers become a bigger segment of the labor market, temporary worker safety is becoming a larger and more critical issue. Host employers have the legal responsibility to provide all workers with safe and healthy workplaces. This requires recognizing the complex issues associated with employing temporary workers and ensuring they are provided the same rights and protections as permanent employees.
More information can be found on temporary workers at the following websites:

Comments: No Comments
Workers’ Rights
Safety Focus
Every worker in the U.S. has the fundamental right to safe and healthful working conditions. The Occupational Safety and Health Administration (OSHA) created the Occupational Safety and Health (OSH) Act for this specific purpose—to establish and enforce workplace health and safety standards that ensure workplace safety and health protection. Correspondingly, it is employers’ responsibility to provide a safe and healthful workplace that is free from serious recognized hazards, per the General Duty Clause of the OSH Act.
It is important for employees to know their rights and understand what to do if a working condition is unsafe or unhealthy. The following common workplace safety concerns address these rights:
- My workplace is unsafe. If you believe you are working in unsafe conditions (e.g., unsafe machinery, exposure to harmful chemicals, poor air quality, etc.), the first step is to bring those conditions to your employer’s attention. Workers may file a formal complaint with OSHA to request an inspection. Each complaint is evaluated by OSHA to determine whether it should be handled as an offsite investigation or an onsite inspection. Employees have the right for their identities to be kept confidential from employers when filing a complaint. If the environment presents risks of serious harm or death, you have the legal right to refuse to work.
- I don’t have the personal protective equipment (PPE) I need to do my job safely. With few exceptions, OSHA requires employers to provide and pay for PPE when it is necessary to protect employees from job-related injuries, illnesses, and fatalities. This may include hard hats, gloves, goggles, safety glasses, welding helmets and goggles, face shields, chemical protective equipment, and fall protection equipment.
- I don’t know what to do if I get injured at work. You have the right (and obligation) to report any work-related injury or illness. If you are injured, call a supervisor for help. If the supervisor is not available, get medical assistance or call 911. Many companies have procedures for injury response. All employers must notify OSHA within 8 hours of a workplace fatality or within 24 hours of any work-related inpatient hospitalization, amputation, or loss of an eye.
- I don’t know what the hazards are at my workplace. OSHA’s Hazard Communication Standard requires employers to inform and train workers about hazardous chemicals and substances in the workplace. This can be done through warning signs, color-coding, signals, Safety Data Sheets (SDS), and training. It is your right to have this information and to receive relevant training in your native language.
- I want to know my employer’s safety record. Current and former employees have the right to get copies of your medical records, see copies of the workplace injury and illness log, and review records of work-related injuries and illnesses. Employers must give the requester a copy of the relevant record(s) by the end of the next business day. In addition, employers must post a summary of the OSHA Form 300 injury and illness log for the previous year where workers can see it.
- I’m afraid to request a safety inspection or speak with a safety inspector. You have the right to request an OSHA inspection and to talk privately with the OSHA inspector before and after the inspection. A worker representative may also go along on the inspection.
- I was fired or threatened for reporting a safety issue. The OSH Act prohibits employers from retaliating against employees for exercising their rights to file a complaint with OSHA. This is known as whistleblower projection. These rights also cover seeking access to employee exposure and injury records, reporting a work-related injury, requesting an OSHA inspection, speaking to the inspector, and alerting your employer of a safety or health complaint. Whistleblower protection prohibits an employer from taking adverse actions against workers for exercising these rights. A whistleblower complaint must be filed with OSHA within 30 calendar days from when the retaliatory decision was made and communicated to the worker.
- Someone is employing children in an unsafe workplace. Federal child labor law generally prohibits employment of minors in nonagricultural occupations under the age of 14, restricts the hours and types of work that minors can perform under 16, and prohibits the employment of minors under the age of 18 in any hazardous occupation (including the use of unsafe machinery). Different child labor law standards apply to agricultural employment.
OSHA is committed to ensuring safe and healthful working conditions for workers by setting and enforcing standards and by providing training, outreach, education, and assistance. More information can be found on workers’ rights at the following websites:
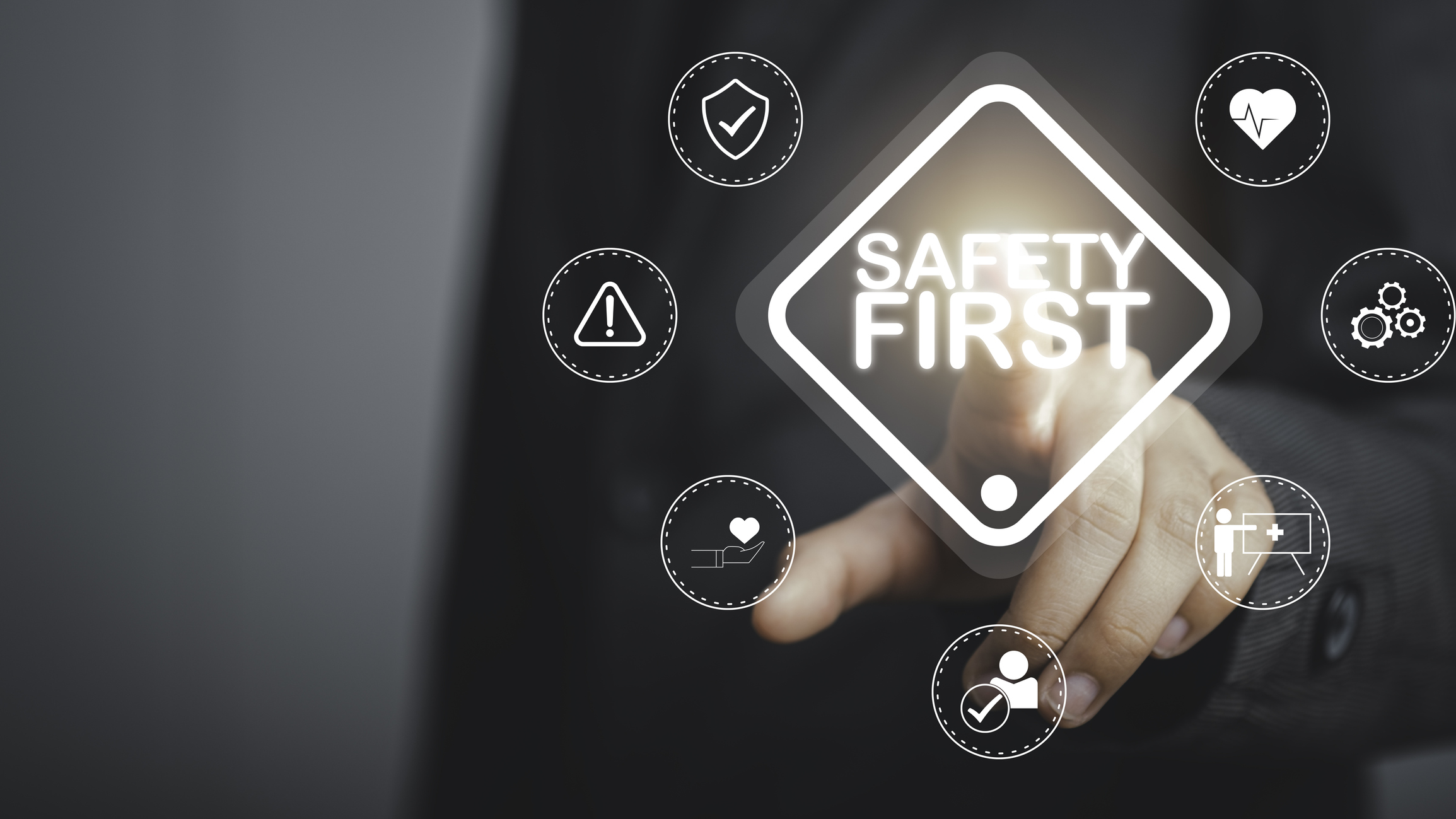
Comments: No Comments
2024 Safety Observations: Putting Safety First
The Occupational Safety and Health (OSH) Act of 1970 was enacted due to the rising concerns over the high rates of workplace injuries, illness, and fatalities in the United States. Prior to the OSH Act, industrial accidents were common. Reports of hazardous working conditions, coupled with the lack of comprehensive federal safety regulations, highlighted the need for a unified approach to workplace safety. During the 1960s, public and labor organizations further demanded better worker protection. The OSH Act was published to address these issues by establishing consistent safety standards, ensuring safer working environments, and reducing the risk of occupational injuries and deaths.
Since the early days of the OSH Act, occupational safety and health has evolved from being a regulatory obligation to being a core component of how successful companies are run. According to the Occupational Safety and Health Administration (OSHA), having a strong safety and health program can help create:
- Fewer accidents, losses, and disruptions by preventing workplace injuries and illnesses.
- Engaged employees and improved morale.
- Increased productivity and enhanced overall business operations.
- Lower workers’ compensation and insurance claims.
- Improved compliance with OSHA regulations.
- Improved reputation to attract new customers and employees and retain existing ones.
- Better brand and shareholder value that tie to social responsibility.
National Health and Safety Observations
Every year, the National Safety Council (NSC), National Institute for Occupational Safety and Health (NIOSH), and OSHA bring additional attention to occupational safety and health issues to help reinforce the importance of having a strong safety culture and to encourage employers and individuals to recommit to working and living safely.
Every June, NSC and NIOSH observe National Safety Month to encourage employers and individuals alike to be safety role models. This year’s focus areas include safety engagement; roadway safety; risk, reduction; and slips, trips, and falls.
Much like National Safety Month, OSHA’s Safe + Sound Week (August 12-18, 2024) is a nationwide event held each August that recognizes the successes of workplace health and safety programs and offers information and ideas on how to keep America’s workers safe. This year’s Safe + Sound Week is focused on providing resources for businesses to conduct Job Hazard Analyses (JHAs).
KTL’s Series on Investing in Safety
Throughout OSHA’s Safe + Sound Week this August, KTL will be featuring a series of articles and posts on our blog and social media (i.e., Facebook, LinkedIn, X) reinforcing these concepts from OSHA, NSC, and NIOSH and discussing why businesses should invest in safety. Topics will include the following:
- Workers’ rights
- Protecting temporary workers
- Psychological safety at work
- Food chemical safety
- Effective safety leadership
Watch for these articles! For more information on what your organization can do to participate and promote a strong safety culture, visit the websites for OSHA Safe + Sound Week and NSC National Safety Month.